Supply Chain and Logistics Definition
A supply chain is a network of businesses and activities that takes a product from raw material suppliers to end consumers. By definition, logistics refers to the processes of acquiring, transporting, and storing resources along the supply chain and logistics. A supply chain, which relies heavily on information technology, logistics and transportation, may involve numerous different businesses that comprise the various links along the supply chain, or a single company may oversee the majority of the supply chain and logistics for its products.
For example, a supply chain for coffee may begin with Central American farmers. The product (coffee) would then move along the supply chain from the farmers to the facilities that process. Then, they package the coffee beans. Then, they would move to distributors that transport the product to wholesalers. These wholesalers might then deliver the product to retailers and neighborhood coffee shops for sale to end customers.
In this example, the supply chain and logistics would be the entire network of businesses that carry the product from its source – the coffee farmers in Central America – to where the finished product is consumed by customers at the neighborhood coffee shop.
Supply Chain and Logistics Activities
Consider supply chain business processes vertical systems. A typical supply chain consists of manufacturers, wholesalers, distributors, and retailers. A supply chain can be seen as a system connecting the value chains of the companies within that system. Consider the activities closest to the source of raw materials upstream activities. Then consider the activities closest to the finished product and the end consumer downstream activities. A company is considered upstream or downstream in relation to other companies in the supply chain depending on its relative position in the supply chain network.
Supply Chain Links
A company will typically participate in a supply chain business process at the point where it can employ its particular functional area of expertise. For example, a trucking company will focus on the transport link of a supply chain, while a mining company will focus on finding and extracting raw natural resources, and retailers will focus on selling the end product to consumers.
Because you can specialize each supply chain link in its own functional area, they may not know about the links directly upstream and downstream from them. That’s why supply chain communication and supply chain coordination, both of which require reliable information technology systems across different businesses, are vitally important to the functioning of a supply chain.
If, however, one link in the supply chain process feels it can expand its responsibilities in the network, either because it can complete a process more efficiently or at a lower cost, then that company can become vertically integrated, by forward integrating or backward integrating. A company that takes over a downstream activity from a customer is forward integrating. In comparison, a company that takes over an upstream activity from a supplier is backward integrating. A company that oversees several consecutive links in the supply chain of its product is vertically integrated.
Supply Chain Management
Supply chain management refers to the process of overseeing and optimizing the overall supply chain network from raw material suppliers to finished product retailers. The goal of supply chain management is to make the supply chain process as efficient as possible by enhancing product and information flows among participating businesses.
Improving your supply chain can involve supply chain communication, or enhance the flow of information among businesses along the supply chain. Furthermore, the logistics and transportation systems will run optimally. But this only happens if all members of the chain have access to all relevant market data and operations information. All other members of the chain provide this information.
Supply chain improvement can also involve supply chain coordination, or optimizing the logistics and transportation activities for maximum efficiency. This may include the following:
- Improving information flows and inter-business communication
- Optimizing manufacturing processes
- Implementing just in time (JIT) production systems
- Optimizing vehicle distribution routes
- Eliminating bottlenecks in the process
- Allocating resources to maximize efficiency
An efficient and optimized supply chain can benefit all the businesses in the supply chain. Therefore, it adds value to the end consumer.
If you want to check if your unit economics are sound, then download your free guide here.
Access your Projections Execution Plan in SCFO Lab. The step-by-step plan to get ahead of your cash flow.
Click here to access your Execution Plan. Not a Lab Member?
Click here to learn more about SCFO Labs
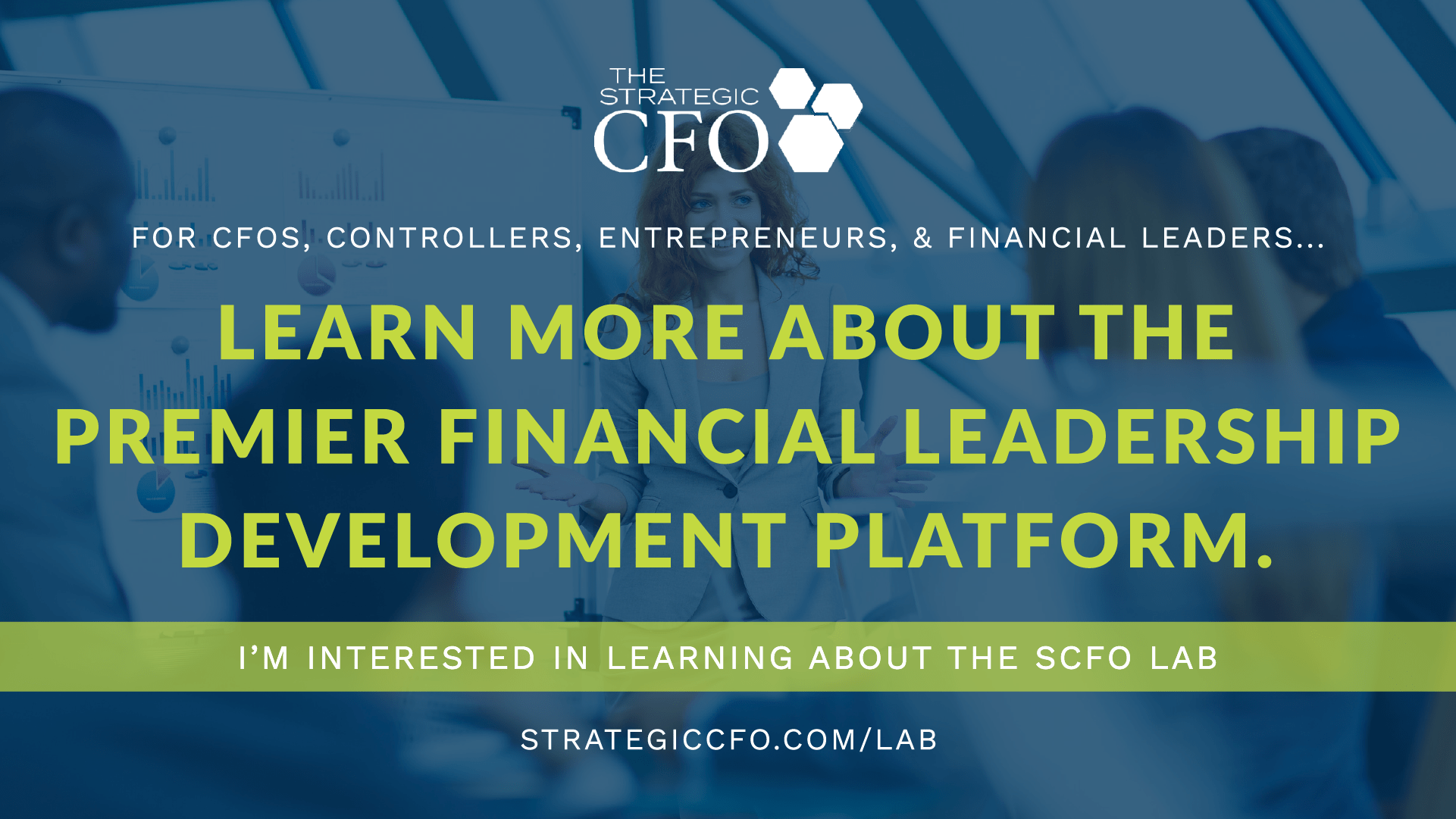
See Also:
Supply and Demand Elasticity
How to Manage Inventory
Perpetual Inventory System
Days Inventory Outstanding Analysis
Inventory Turnover Ratio Analysis