See Also:
Inventory Turnover Ratio
Perpetual Inventory System
Just in Time Inventory System
Inventory to Working Capital Analysis
Value Drivers: Building Reliable Systems to Sustain Growth
Just in Time Inventory System Definition
The just in time inventory system, or JIT, is a system of managing inventory that is designed to improve efficiency and reduce waste in a production process, and minimize inventory carrying costs. The idea is to receive production inputs only as needed in the production process. To implement the just-in-time system, a company must establish tight coordination with its suppliers.
Ideally, a company employing the just-in-time system would have no on-hand inventory. It costs money to hold inventory. The just-in-time system aims to eliminate that cost. A production process using the just-in-time system would receive the correct type and quantity of material inputs at the precise time the inputs are needed in the production process. Depending on the process, the just-in-time system may require multiple material deliveries from suppliers per day. This system requires a closeness – in terms of profession relations as well as geographic proximity – with suppliers.
Download The KPI Discovery Cheatsheet
Advantages and Disadvantages
The primary advantage of the just-in-time system is the reduction of inventory carrying costs. If implemented correctly, then it also improves operational efficiency and reduces waste. The primary disadvantage is the system’s susceptibility to disruption. A defective input or a process break-down can be very problematic. This requires anticipation and correction of potential problems before they occur.
Push vs Pull System
Consider traditional inventory and production systems “push” systems. Then consider a just-in-time system a “pull” system.
In a push system, the company forecasts demand, prepares a production schedule, and then orders inputs to begin the production process. The result is a build-up of inventory. It is intended to be ready for sale and delivery to customers. Inventory is “pushed” through the system to the customer.
In a pull system, the company waits to receive a customer order. When the order comes in, the company requests only the necessary inputs for that particular order from its suppliers. Then the company makes the product. When complete, the company ships the product out to the customer. The inventory is “pulled” through the system by the customer order.
Access your Flash Report Execution Plan in SCFO Lab. The step-by-step plan to create a dashboard to measure productivity, profitability, and liquidity of your company.
Click here to access your Execution Plan. Not a Lab Member?
Click here to learn more about SCFO Labs
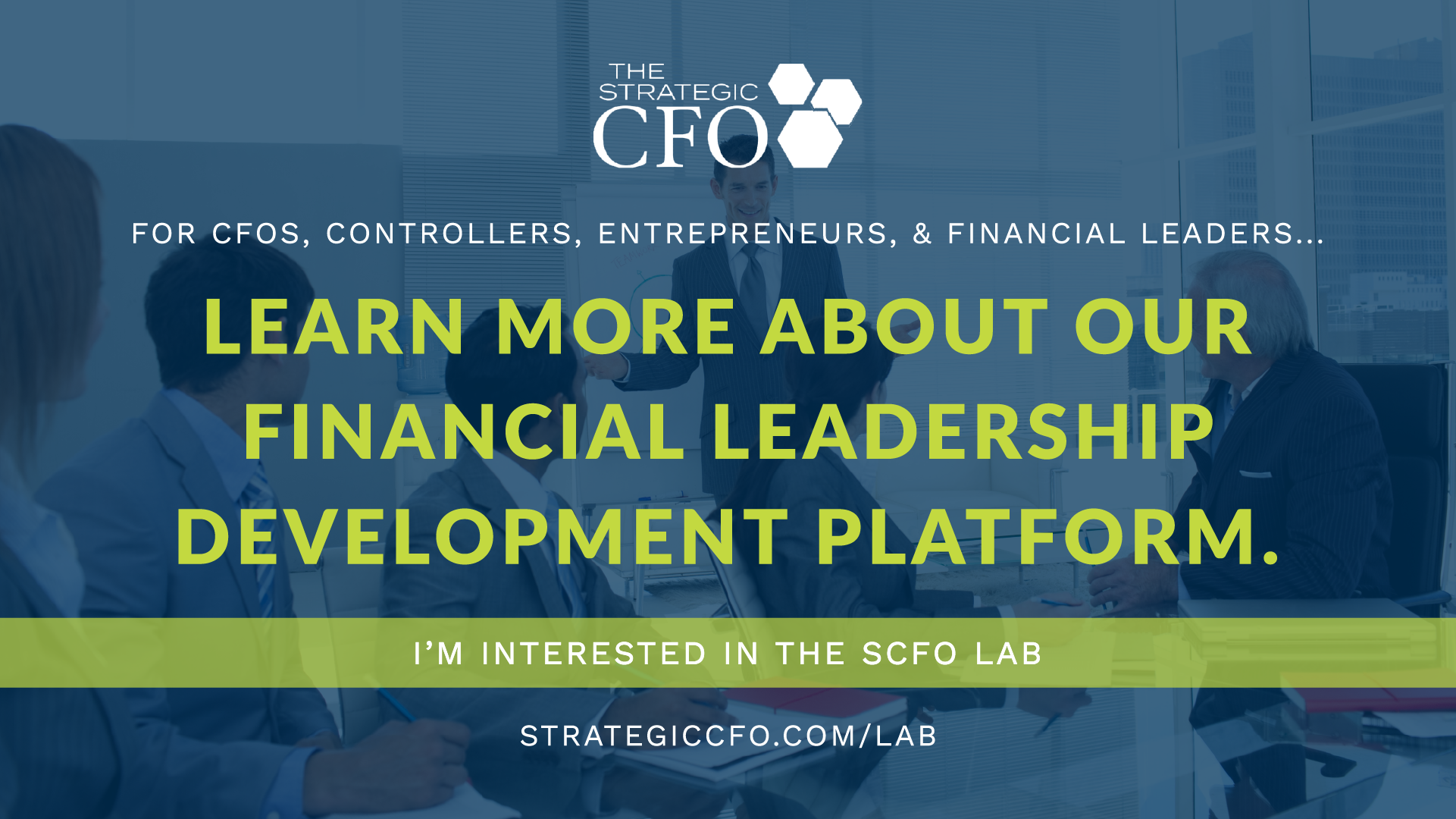